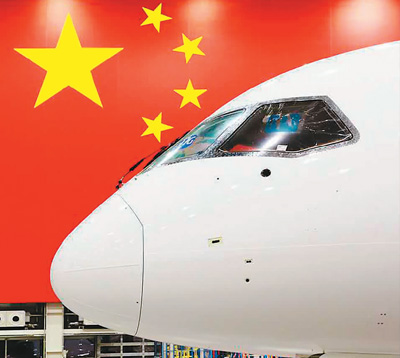
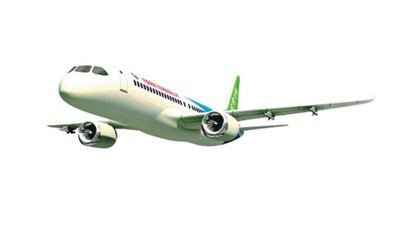
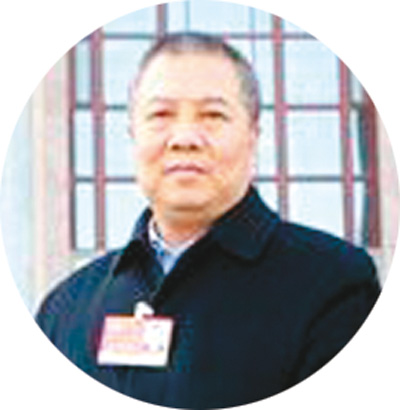
Wu Guanghui, chief designer of Comac C919 and ARJ21, has won the national special prize for scientific and technological progress and the first prize for national defense scientific and technological achievements. A key model won the first prize of China Aviation Industry Corporation I and the first prize of the National Defense Science, Technology and Industry Committee.
"Many aircraft parts are made in China and fly in the sky every day. C919 has gone through nearly seven years, and has done a lot of design, calculation and experiments. I am definitely willing to take this plane first. "
— — Wu Guanghui
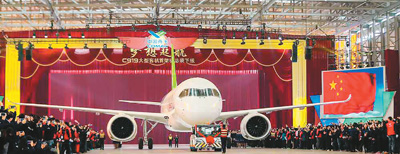
These days, in the commercial aircraft test center of China Commercial Aircraft Corporation, the newly-built Zhuqiao test hangar in Pudong is spacious and bright. In the hangar, the landing gear that originally supported the domestic large passenger plane C919 was all put into the landing gear cabin, and three air springs like "jacks" lifted the plane into mid-air. What is going on here is the ground resonance test and modal coupling test of the whole aircraft that must be completed before the first flight, which means that the C919 has officially entered the final sprint stage before the first flight.
C919 is a domestic large passenger plane independently designed and developed by China. It is a short-haul single-aisle narrow-body passenger plane with more than 150 seats. In the future, it will compete with internationally renowned commercial aircraft such as Airbus 320 series and Boeing 737 series for orders. The manufacturer China Commercial Aircraft Co., Ltd. recently announced that the C919 plans to make its first flight in the first half of 2017 and will fully launch the wide-body passenger aircraft project. It can be said that after nearly 10 years of hard work, China people’s dream of "big plane" will soon become a reality.
① Rigorous test to ensure safety.
To fly into the blue sky, a plane must first practice a pair of steel bars and iron bones. For the C919, which carries the dream of a big plane for Chinese people, the significance of the test is even more significant. This is the first large passenger plane made by China people, and its safety cannot be lost.
For this reason, C919 has undergone a series of tests like "torture". Among them, the 2.5g static test of the whole aircraft started in early November last year is the most severe and significant one since the birth of the C919.
This test mainly tests the strain and deformation of the "skeleton" of the body under constant external loading. In layman’s terms, this kind of test is to let the aircraft simulate the stress situation when challenging air flight on the ground, and go beyond the natural limit to verify how much force the aircraft can bear.
Before the start of the experiment, the researchers covered the whole body with white adhesive tape, which is a resistance strain gauge that can sensitively measure stress and strain close to the surface of the body, just like doing electrocardiogram for the plane. During the test, the load starts to rise at the level of 5%, and the load must be kept for 3 seconds every time. "The structure must be able to withstand the ultimate load for 3 seconds without damage." Zhou Liang Dao, deputy chief designer of the C919 passenger plane, said that the preparation behind the team took more than 300 days for this short three seconds.
With the continuous loading, the aircraft began to show obvious external reflection, and the wing began to tilt up a little. Finally, when the load reaches 100% of the test outline, the wing tip tilts up to nearly 2 meters, which is highly consistent with the strength analysis before the test, which shows that the test is successful and its strong "bones" and body are enough to support flying into the blue sky.
This is just a small step in the long March before the first flight of the plane. A passenger plane has to complete 13 static tests in 48 working conditions, including pressurization in the booster cabin, front lifting connection, main lifting connection, whole aircraft condition, vertical tail and rudder, as well as "three-bird test" such as iron bird, copper bird and electric bird and joint test of the whole aircraft system. Therefore, researchers have made independent innovations in system integration experiments.
In the comprehensive test hall of Shanghai Aircraft Design and Research Institute, the iron bird test-bed with little difference from the C919 real machine looks like an eagle with wings spread and its tail stuck high. Don’t underestimate this test-bed. Its full name is "Integrated Test-bed for Flight Control Hydraulic System", which mainly tests the landing gear, wings and other mechanical systems of aircraft. In order to ensure the authenticity of the system test, the iron bird test-bed is designed according to the 1:1 ratio of the real aircraft, so that the mechanical installation interfaces of the flight control, hydraulic and landing gear systems are the same as those of the aircraft.
Next to the Iron Bird Test Bench, there is also a "Copper Bird" that tests power supply systems such as power generation and distribution, and also restores the real state of the machine to 1:1 for equipment installation. "Iron Bird", "Copper Bird" and the avionics system test called "Electric Bird" will eventually be all connected, thus forming a "three-bird joint test" to simulate the state of the aircraft.
In the experiment, researchers conducted a comprehensive test on the aircraft system. Take the avionics system as an example. At most, there are more than 100,000 parameters in a test. These parameters should be tested one by one to find out the possible omissions in the design. "Our goal is not to take the fault to the sky." Yu Shenghui, senior engineer of the General Aerodynamics Department of Shanghai Aircraft Design and Research Institute, said.
According to the plan, six testing machines are carrying out joint testing of the whole machine system, and customer service engineering and airworthiness work are also being carried out simultaneously.
②C919 is genuine China goods.
As the first large passenger plane with completely independent intellectual property rights in China, C919 has been frequently questioned since it was established in 2006: an aircraft whose engine, avionics core processing system and some materials all depend on foreign products or technologies, why should it be said to be "made in China"?
In fact, to evaluate the innovation of C919, we may need to draw lessons from a fairy tale named Pony Crossing the River. This story is about a pony crossing a river. A cow next to it said, "The water is very shallow, just without a calf, so you can cross it." But the squirrel in the tree said, "The water is deep and will drown." So, is the river deep or shallow? Finally, the pony got off the river by himself and carefully waded to the other side. It found that the river was neither as shallow as the cow said, nor as deep as the squirrel said. The same is true for the development and innovation of C919. Everyone should not only see the major innovations achieved in the process of aircraft development, but also objectively admit the existing shortcomings.
According to international standards, judging whether an airplane is made in China or assembled depends on whether it meets three conditions. 1. Who owns the property right of the whole machine? Second, who is the core team to develop the whole machine? Third, who holds the key link in the development of the whole machine? For C919, the answer to these three questions is China.
The person in charge of Comac in China said that the property right of the C919 is owned by Comac in China. The team of Comac in China is the core of the development, and the key links such as aircraft design, final assembly, test flight and sales are in the hands of Comac in China.
As for foreign companies providing parts or technology, this is a common thing in the global aviation manufacturing industry. Aviation manufacturing giants such as Boeing and Airbus also use foreign products on many key components when developing aircraft.
However, for equipment like engines, the C919 chose the LEAP-X1C engine jointly developed by the United States and France, which is the only foreign starting power device selected by the C919. It should be said that the engine is indeed a major constraint in the development of China’s large aircraft, and it can only be sought from people at present. However, I believe that in 10 to 15 years, China will be able to develop its own advanced aero-engine for large aircraft.
③ Have a number of scientific and technological innovations.
Experts said that the C919 was completely designed and integrated independently, with outstanding technical indicators. It is the persistent innovation of researchers who have sharpened their swords for ten years that has led to the high-tech C919, which integrates many key technologies.
However, what did C919 look like when it was approved as one of the 16 major projects in the national medium-and long-term science and technology planning in January 2006? What difficulties may be encountered in the development? Due to the limitation of western aviation powers in technology introduction, China researchers have no idea and can only cross the river by feeling the stones.
In November 2008, the C919 project was launched. A large passenger aircraft joint engineering team composed of 468 experts from 47 domestic and foreign units, plus a large passenger aircraft expert consulting group composed of 20 academicians and experts, started from sketches and gradually sorted out the first batch of 14 special technical research projects that need to be started.
Among these key technologies, there are several that must be mentioned. For example, the "supercritical airfoil" that makes airplanes more fuel efficient. A large passenger airliner is an out-and-out "oil tiger". In order to reduce fuel consumption, the wing design of C919 uses a supercritical airfoil, which improves the cruise aerodynamic efficiency by more than 20% and reduces drag by about 8%.
Another unique innovation is the adoption of the third generation Al-Li alloy materials. It is the first time in China that the world’s advanced third-generation Al-Li alloy materials are widely used in the main structure of C919. Compared with ordinary aluminum alloy, this lightweight metal material with high damage resistance has greater strength and lighter weight under the same strength, which is very important to realize the weight reduction of aircraft structure and greatly improve the service life of aircraft.
In addition, as the "brain" of the C919, the avionics system of the aircraft has realized "giving all the work to the network". Compared with the old version of the network, which was widely used before but had limited bandwidth, the new aviation bus communication protocol adopted by C919 not only has high bandwidth but also shares resources, which means that the signals that originally needed to be transmitted through several cables can now be transmitted by one cable. Experts said that this is like we need to run 10 trains from A to B, but we don’t need to build 10 railways. We only need a set of double-track railways and a reliable signal system.
According to Wu Guanghui, the chief designer of C919, the developers have planned 102 key technical problems, and many advanced materials have been applied on a large scale in domestic civil aircraft for the first time. The development process of millions of parts and airborne systems is highly parallel. In order to overcome these technical difficulties, 22 provinces and cities, more than 200 enterprises, 36 universities and hundreds of thousands of industrial personnel participated in the development of C919 large passenger aircraft, and 16 material manufacturers and 54 standard parts manufacturers including Baosteel became suppliers or potential suppliers of large passenger aircraft projects.
Our reporter Peng Xunwen